Other
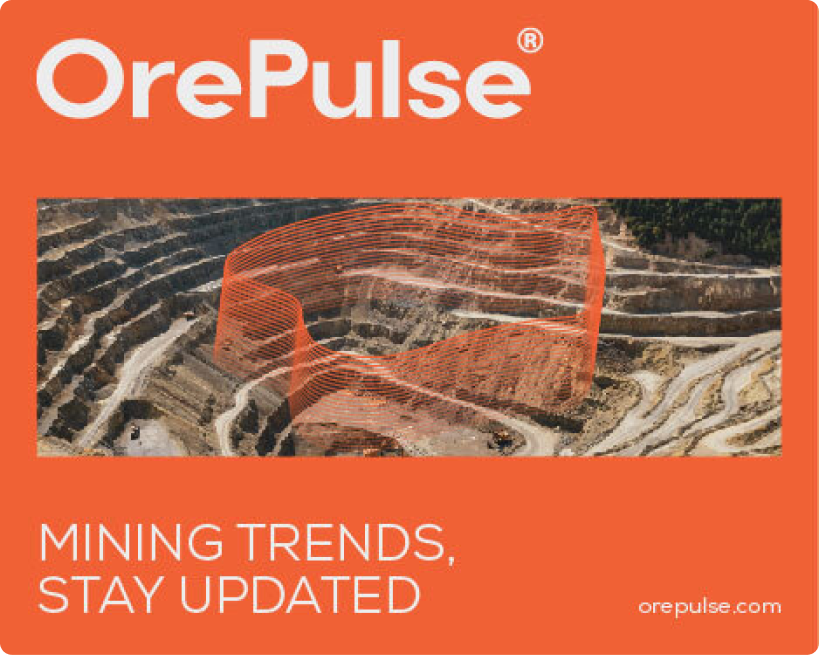
A walk through innovation – for sustainability at its best at Electra Mining Africa
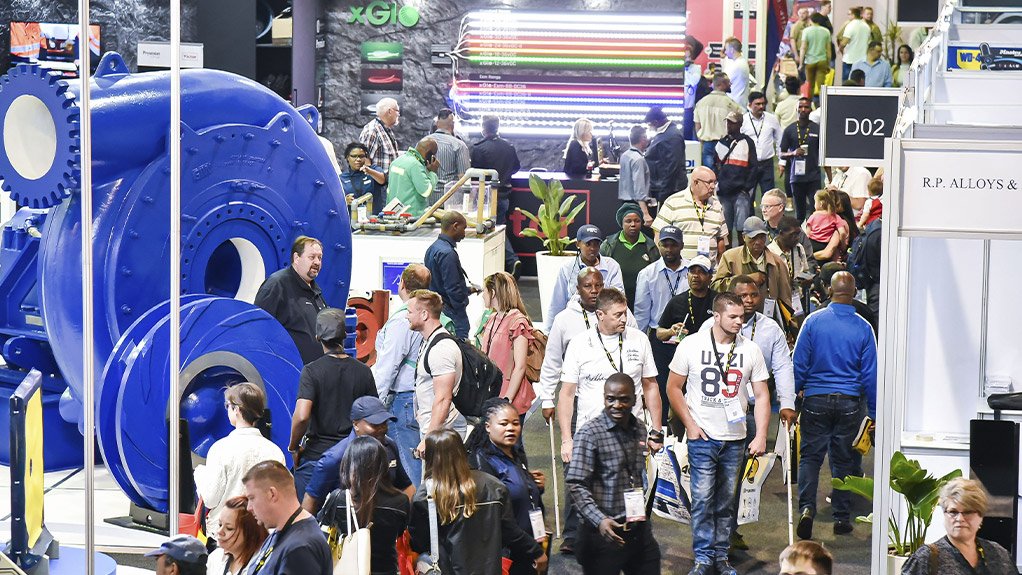
In the first week of September 2024, Electra Mining Africa connected people, products, services and innovation across industries and across borders in southern Africa, and the impact of the combined collaboration and innovation showcasing, and knowledge sharing on the South African economy and the African region will reverberate for months to come.
The mining, electrical, automation, power and transport industries collided spectacularly, re-igniting inspiration in all sectors with an energy difficult to describe at the face-to-face, 5-in-1 interconnected tradeshow experience with manufacturing at its core.
Join African Mining on an excursion through the tradeshow, spot lighting just some of the innovations celebrated this year, many of which were involved in the New Products & Innovations awards, organized in partnership with the South African Capital Equipment Export Council (SACEEC), talked celebrated at the event. When presenting the awards, Eric Bruggeman, CEO of SACEEC and co-adjudicator with mechanical engineer Tristen Wintershoven, said, “The New Products & Innovations awards at Electra Mining Africa are now internationally recognized.”
On the evening of Wednesday 4 September, mid-expo and at the awards ceremony, Gary Corin, managing director of Specialized Exhibitions – the largest trade exhibition organizer in southern Africa and a division of Montgomery Group – said, “I’ve been in the company nearly 30 years, and what you have seen out there over the past three days is the best that I’ve ever witnessed here in my life. It’s a record – no matter what metric we use – 40 000 square meters in space, 950 odd exhibitors – 94% local, 6% international. Over the last three days, 22 200 visitors versus 15 000 this time two years ago, have come to witness innovation in industry!” By the end of the event at close of business on Friday, 6 September – 39 883 visitors had attended the tradeshow to observe the innovation showcased. We invite you on a virtual tour of the show, where African Mining was able to interview some of the innovators and change-makers in this 2-part article series.
A global first for safety
Exhibitor, Intuit group stood out, not only as a New Products & Innovations awards winner for a locally manufactured innovation, but also for a world first invention of IoT technology that attaches to a working-at-heights harness. This solution provides real time telemetry information while working at heights to monitor climbing performance. “It records hooking and unhooking and the time it takes in-between, notating where double unhooking, for instance, takes place – which is absolutely not allowed because it’s a critical control,” said company, executive Michael Gouws.
This invention supplies information directly “from the field to the fingertips” of a supervisor or mine manager to enable them complete management of workers on site, allowing them peace of mind that workers are following safe working practices, and enabling them to intervene with training where necessary, before an incident occurs.
The system comprises the harness clip, a sensor and a digital dashboard relaying and displaying information that is collected from the sensors, which monitor the worker’s movement on the job. It is a tool that aids visibility and provides tactile feedback to promote safe behavior.
Electrical excellence
Another local innovator, electrical engineer and owner of AZTEC – a 45-year-old South African engineering company operating predominantly in the mining industry – Dean Marcus took African Mining through their winning solution in the local manufacturing, electrical category, “We’ve developed the Mini Start system for underground miniature substations with motorised switch gear. The unit eliminates the need for UPSes, batteries and voltage transformers, which can be dangerous to those operating the minisub after a power failure.”
Intelligent conveyors
Winner in the international manufacturing, ITC category, Tru-Trac, unveiled the Rip Prevent+ system at Electra Mining Africa which could “revolutionize conveying system around the world,” per Jonathan Rogoff – CEO. This monitoring technology is set to disrupt the sector using a data-driven model and artificial intelligence (AI) to detect anomalies or rip events on any conveyor belt type, including metal cord, pipe and fabric belts – minimizing downtime and enhancing efficiency and productivity.
The system, already proven effective in global mining operations, is now available in Africa, allowing mines to optimize their conveyor lines’ performance by preventing costly interruptions due to rip events. It was designed to avoid the need for sensor elements inside the belt – analyzing data from the conveyor belt using AI and combining with an innovative algorithm, it detects anomalies and generates data and signals that allow customers to stop the conveyor line before significant damage occurs. The system’s model computes data 50 times per second and can generate a signal to the Programmable Logic Controller (PLC) within 0.2 seconds, reducing the impact of rip events.
By stopping the conveyor belt when a possible rip event is detected, the system minimizes associated damage, potentially saving millions in downtime, belt replacement, and cleanup costs. The system’s data-driven model offers significant advantages over inductive, magnetic and laser-based systems including reduced wear risk, suitability for all conveyor types and lower investment costs.
The Rip Prevent+ system is web-based and accessible via an Ethernet network connection, featuring a user-friendly interface with a dashboard displaying key information. Additionally, the system incorporates several functions beyond rip detection, including mass flow calculation, condition monitoring, drive or motor monitoring, energy efficiency and electrical network analysis, aligning with predictive maintenance strategies. It is also easy to install, requiring only 30 minutes to an hour, with minimal downtime for electrical connections. Commissioning the system can be completed within two to five hours, depending on preparatory work and available system parameters.
Notably, Rip Prevent+ is the first rip detection system offering a more affordable alternative through a subscription model that minimizes initial capital investment.
Pumping without electrical power
Mark Enel, sales manager at RNE Pumps, explained the innovation that won them the new the New Products and Innovation Award for the industrial section in the local manufacturing category, “We found is that there are areas in the world that do not have access to three phase power for one, and our electrically driven vertical spindle pumps range was also being underutilized in industry because of this lack of power. So, we came up with an idea to develop a system that doesn’t need electrical power and we created a diesel-engine, hydraulically operated Salter Pump.” The pump is a vertical spindle pump mounted on the back of a trailer, which can be positioned wherever dewatering needs to take place. Designed to operate 24 hours, nonstop, before a diesel refill is required – these pumps can be customized to “fit” the application.