Other
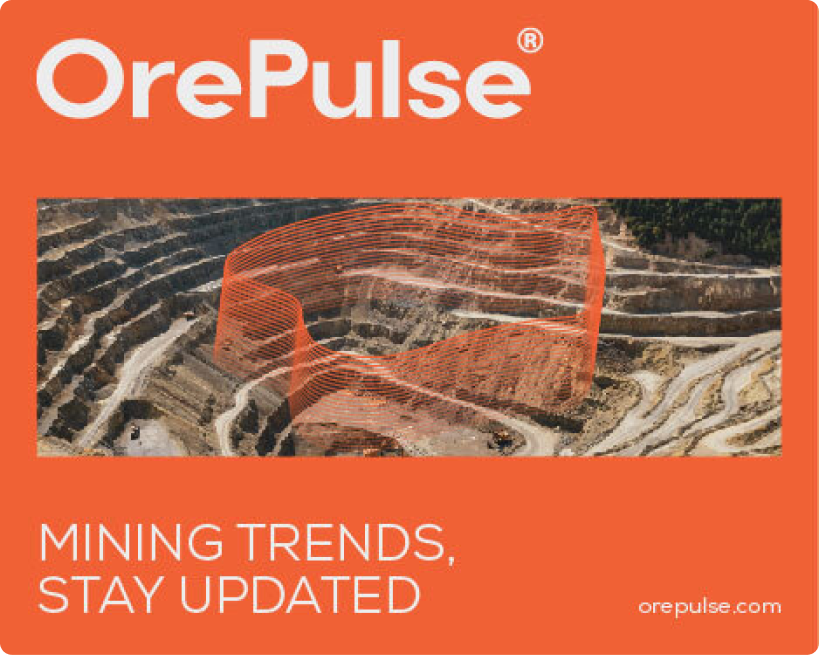
South Africa’s palladium can cut South Africa’s water treatment costs, researchers show
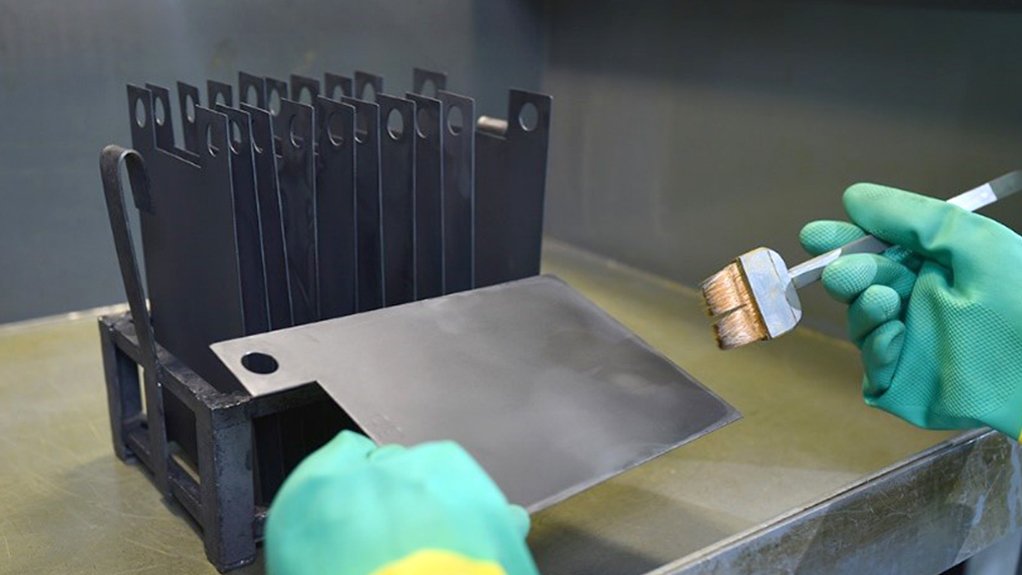
Now, three months later, Izotov has popped up with a tested palladium development that is saving a water treatment site $150 000 a year and is also earmarked for seawater applications in coastal power plants and desalination facilities, which could potentially be applied at South Africa's progressing $5.8-billion green-hydrogen-linked Coega Green Ammonia Project being developed in Nelson Mandela Bay.
The water treatment saving reported is the result of a palladium-coated electrode cutting energy consumption in the production of sodium hypochlorite, the widely used disinfectant in municipal water treatment systems.
Palladium’s distinctive catalytic activity enables greater sodium hypochlorite output from the same amount of electricity, which means more water can be disinfected with lower energy input.
In South Africa, where sodium hypochlorite is widely used and electricity costs are high, adopting energy-efficient anodes could help reduce operating expenses for water utilities and municipalities, the release points out.
This is particularly relevant in countries with expensive or limited electricity supply such as South Africa but which is also endowed with abundant locally mined palladium.
“These electrodes could drive demand for 5 t of palladium in the near future, representing a significant growth factor for the metal beyond its traditional automotive sector applications,” Izotov points out in a media release to Mining Weekly.
The technology is compatible with global sodium hypochlorite generation systems, and serial production has already begun.
Local sodium hypochlorite service providers are showing interest in alternative electrochemical technologies that optimise costs without compromising water treatment quality. Also highlighted is that lowering energy consumption eases strain on aging infrastructure and improves resilience during power outages.
The palladium-coated electrodes have been found to lower the operating voltage of electrolysis units by 5% to 7%, resulting in an 18.6% reduction in energy costs when compared with traditional anodes based on metals that include iridium, which South Africa also produces but which is a very scarce platinum group metal (PGM) and great effort is being made to thrift it owing to its increasing demand for green hydrogen generation.
The durability of the electrodes is also fortified by the incorporation of palladium into the coating.
The first commercial batch of 560 palladium-coated electrodes deployed at a regional water supply operation have reportedly been operating successfully for more than six months.
The palladium coating is said to improve catalytic selectivity toward active chlorine and enhance corrosion resistance, which extends electrode life and lowers maintenance costs.
At the PGM Day, Nornickel reported that it was opening a large, globally collaborative palladium laboratory, as part of its new 100-patent Palladium Center, which is striving to change how the world sees palladium.
The centre has been working with ECOFES, a Russian company specialising in water treatment technologies, particularly systems for purification of drinking water and industrial wastewater.
According to ECOFES, the new coating improves catalytic selectivity toward active chlorine and enhances corrosion resistance, which extends electrode lifespan and reduces maintenance costs.
“Our goal was to deliver industrial-level efficiency for on-site sodium hypochlorite production without increasing costs,” says ECOFES founder Lev Fesenko, who is negotiating with international partners and testing the technology for seawater applications, such as coastal power plants and desalination facilities.
In South Africa, where sodium hypochlorite is widely used and electricity costs are high, adopting energy-efficient anodes could help reduce operating expenses for water utilities and municipalities.
Local service providers are showing interest in alternative electrochemical technologies that optimize costs without compromising water treatment quality. Analysts also highlight that lowering energy consumption will ease strain on aging infrastructure and improve resilience during power outages.
South African PGM companies have been invited to become part of a programme that is targeting an initial 1.7-million-ounce increase in demand for palladium
By 2030, the Palladium Center’s portfolio is expected to advance beyond 100 projects, generating an additional 1.7-million-ounce annual palladium demand.
“We aim to share expertise and collaborate with those who, like us, see palladium as a metal of the future,” Izotov emphasised during the visit to South Africa, which was part of a global roadshow aimed at combining research and business efforts to drive sustainable development.
From a chemical perspective, PGMs complement each other in many applications and research shows that palladium alloyed with other PGMs frequently outperforms the efficiency and durability of individual PGMs.
Other potential new palladium applications highlighted in Johannesburg included:
- using a layer of palladium to minimise the light loss of solar panels;
- upgrading hydrogen fuel cell performance;
- lowering green hydrogen production costs;
- replacing scarce iridium with palladium inorganic light-emitting diode (OLED) displays; and
- deploying palladium-based alloys to reduce conductive component expenses in electronics.
A palladium layer in silicon solar cells is expected to provide a 2%-plus efficiency uplift owing to reduced light reflection and absorption compared with silver-enhanced photon capture. There is also said to be less microcrack propensity.
Palladium-platinum alloy is said to provide 10%-plus optimisation in hydrogen fuel cell catalysis and proton exchange membrane (PEM), plus a PEM replacement cost reduction of 10% to 25%.
When it comes to OLED displays, palladium use is said to reduce costs by 50% to 70% and increase the lifespan of blue OLEDs by 50%.
Palladium is reputed to have a great future from a chemical standpoint. PGMs are substitutes and complementors. Experiments signify that PGM alloys tend to improve efficiency and lifespan.
Because PGM alloys complicate recycling, work is being done with PGM refiners to simplify and optimise the use of scrapped PGMs.
The Palladium Center is setting out to find the prospective projects where it is already very clear that palladium will make a competitive contribution.
It produces the prototype, arranges end-user testing, analyses feedback, provides product upliftment, and then bestows licensing to the producers of the PGM materials.
At the outset in 2021, there were no AI solutions but by end of 2024 about 80% of equipment was operated by computer vision algorithms, and at operational level, the company’s biggest mining mill is functioning automatically on machine learning.