Other
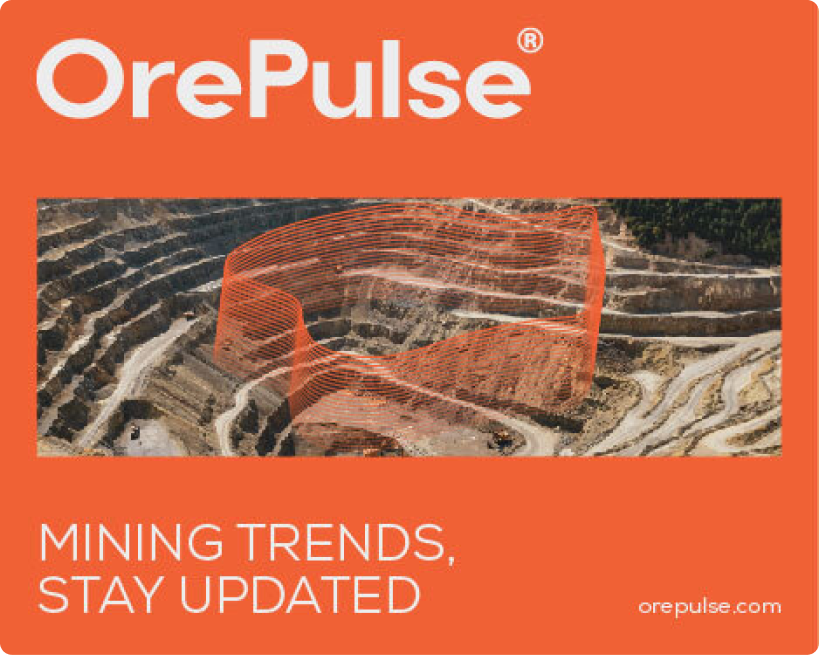
Collaborative, integrated solutions from SKF boost production for prominent mining operation in Zambia
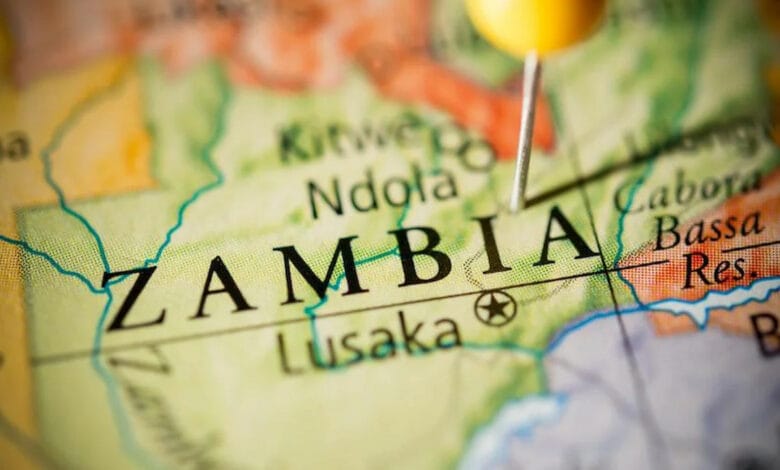
Chronic critical bearing failures on a ball mill were hammering production and driving costly downtime, prompting one of Zambia’s leading copper mines to turn to SKF for a sustainable solution.
Excessive vibration and extreme temperatures at both the feed and discharge ends of the mill were identified by SKF specialists as the root cause of the bearing failures.
Early fault detection and proactive maintenance are key to preventing premature equipment failure, underscoring the need for a condition monitoring solution. SKF recommended the Multilog IMx-16 condition monitoring system to the customer. “This compact, versatile device delivers critical insights into machine and equipment health, offering immense value that can be quantified in both time and cost savings,” states Mel Patel – Regional Sales Manager CEA for Heavy Industries Business at SKF Zambia.
The 16-channel system was installed on the ball mill for continuous monitoring. “The data gathered by the system’s 16 sensors is automatically stored and shared on the SKF Cloud and is monitored and analysed by SKF Remote Diagnostic Services (RDC/REP) in South Africa, giving proactive reports and alarms,” explains Patel. “These reports and expert recommendations and advice, enable our mine customer to correct existing or impending conditions and schedule any required maintenance.” He adds that the Multilog system also has the capability to provide data to the customer’s historian (data store) for machine learning algorithms and analytics.
The scope of work also called for three off 248/1800 bearings and the design of new feed end (FE) and discharge end (DE) housings. The housing designs as well as the mounting/dismounting of the bearings were facilitated by SKF Zambia’s Chitalu Mwape – Key Account Manager Mining, Tonny Luwo – Regional Customer Experience Manager CEA and Kutsi Jaka – Product Manager: Condition Monitoring, alongside Darrin Cardoso – Application Engineer / Key Account Manager Cement and Paul Bekker – Services Manager: Bearings, both from the SKF South Africa office.
“We held regular meetings with our customer and established an active group chat to ensure real-time communication with all stakeholders,” affirms Patel. “Thanks to the proactive collaboration of our team, including RDC/REP, the Application Engineering team and service technicians, we delivered measurable cost savings for our customer by combatting bearing failures, maximising equipment performance, significantly increasing uptime and boosting production output.”
He further highlights that extending equipment service life not only enhances operational efficiency but also provides to sustainability benefits by reducing waste, conserving resources and minimising the environmental impact of frequent replacements.
In closing, Patel remarks that the success of this project stands as a clear demonstration of the power of collaboration of the SKF regions across the African continent, integrating product, services and engineering. It highlights the collective strength, expertise and commitment of the teams working together to achieve a common goal, to provide the customer with a solution that not only meets current needs but also ensures a sustainably successful and efficient operation.